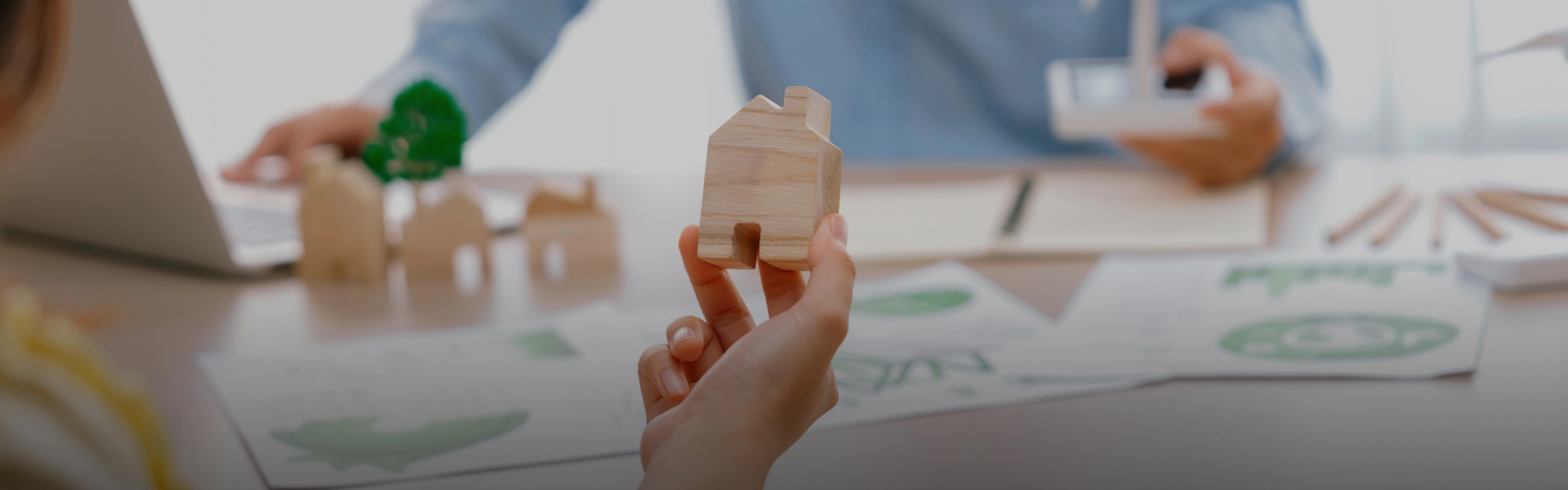
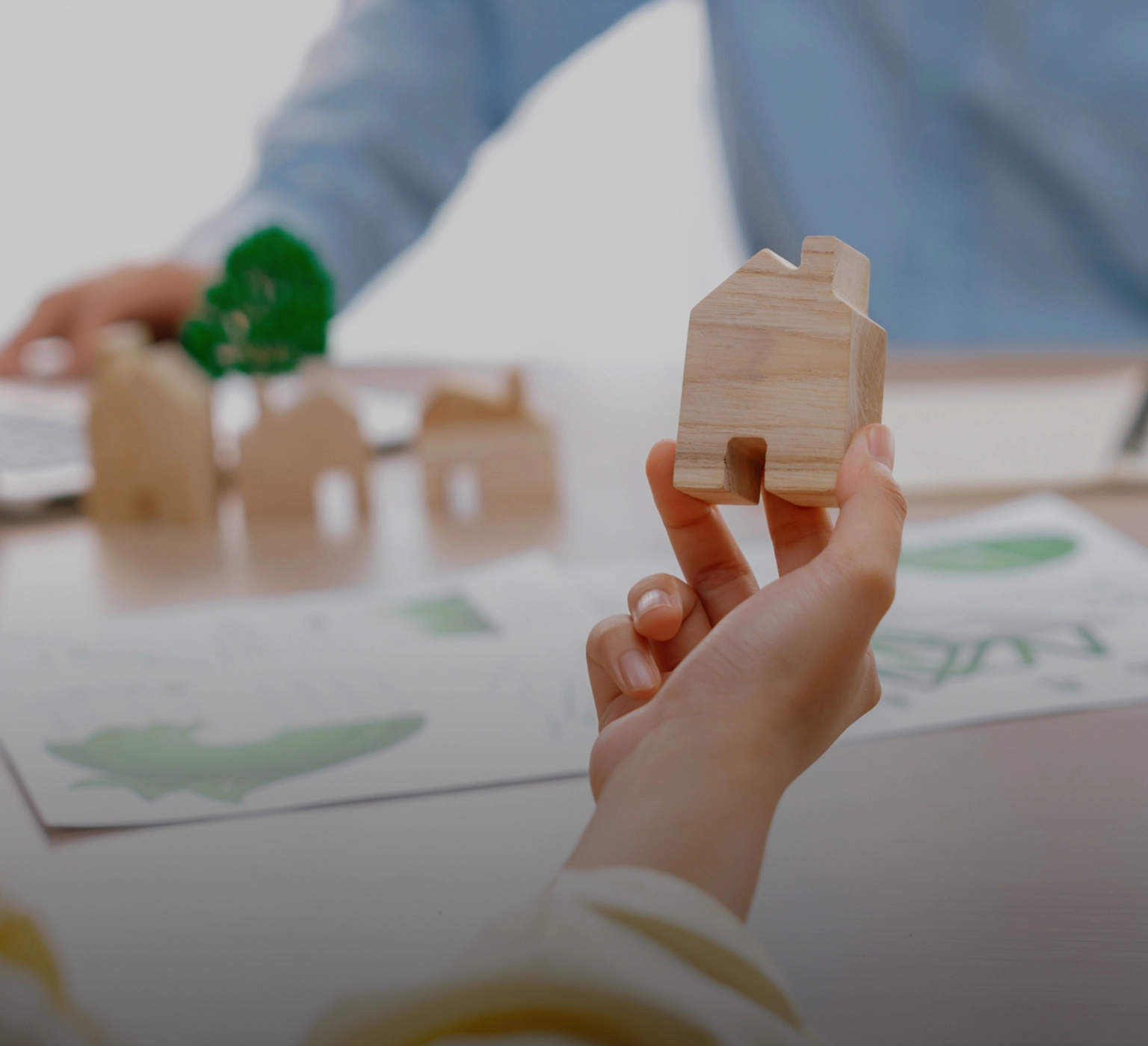
Product Quality and Safety
Commitment, Challenge and Opportunity
CH. Karnchang engages in construction and large-scale infrastructure investment, emphasizing high-quality materials, energy efficiency, resource conservation, and environmentally friendly practices while maintaining strict construction oversight.
These efforts build trust among stakeholders, including customers, communities, employees, and investors. The company prioritizes safety, sustainability, and environmental responsibility at every stage, aiming to minimize environmental impact and workplace risks, foster a positive work environment, reduce operational costs, and strengthen its reputation and brand image. Upholding quality standards enhances confidence and increases company value, ensuring long-term stakeholder satisfaction.
Supporting the SDGs Goals
Goal 11:
Goal 12:
Goal 13:
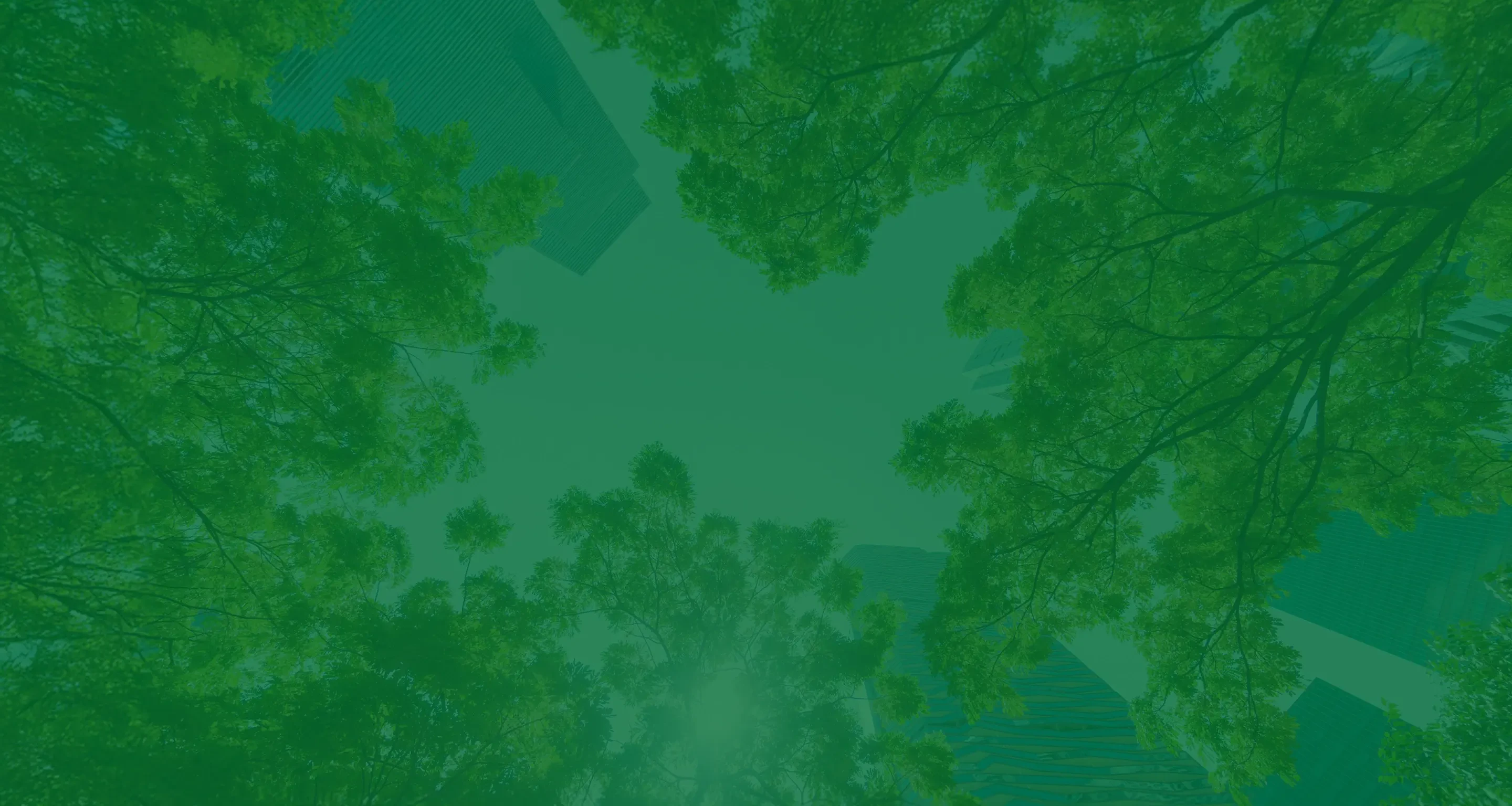
Stakeholders Directly Impacted
Goals and Performance Highlights
- Use environmentally friendly materials for at least 10% of the project's total material cost.
- Concrete must contain at least 20% recycled materials and be made entirely from local materials.
- Rebar and structural steel must contain at least 90% recycled materials and 90% locally sourced materials.
- Lightweight bricks and Mon bricks must be made entirely from locally sourced materials.
- Minimize construction waste in accordance with TREES NC Credit MR 2 by reusing or recycling at least 50% of the waste by weight and volume.
(However, the team aims to reduce waste by more than 75%)
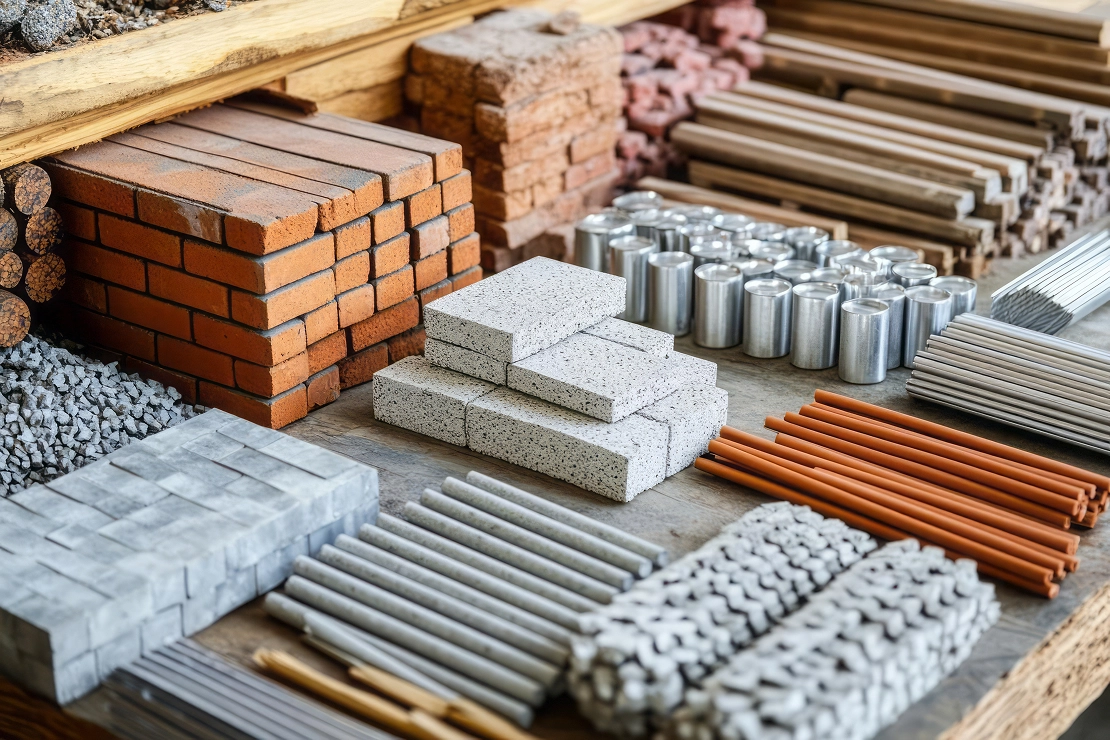
Management and Operational Approach
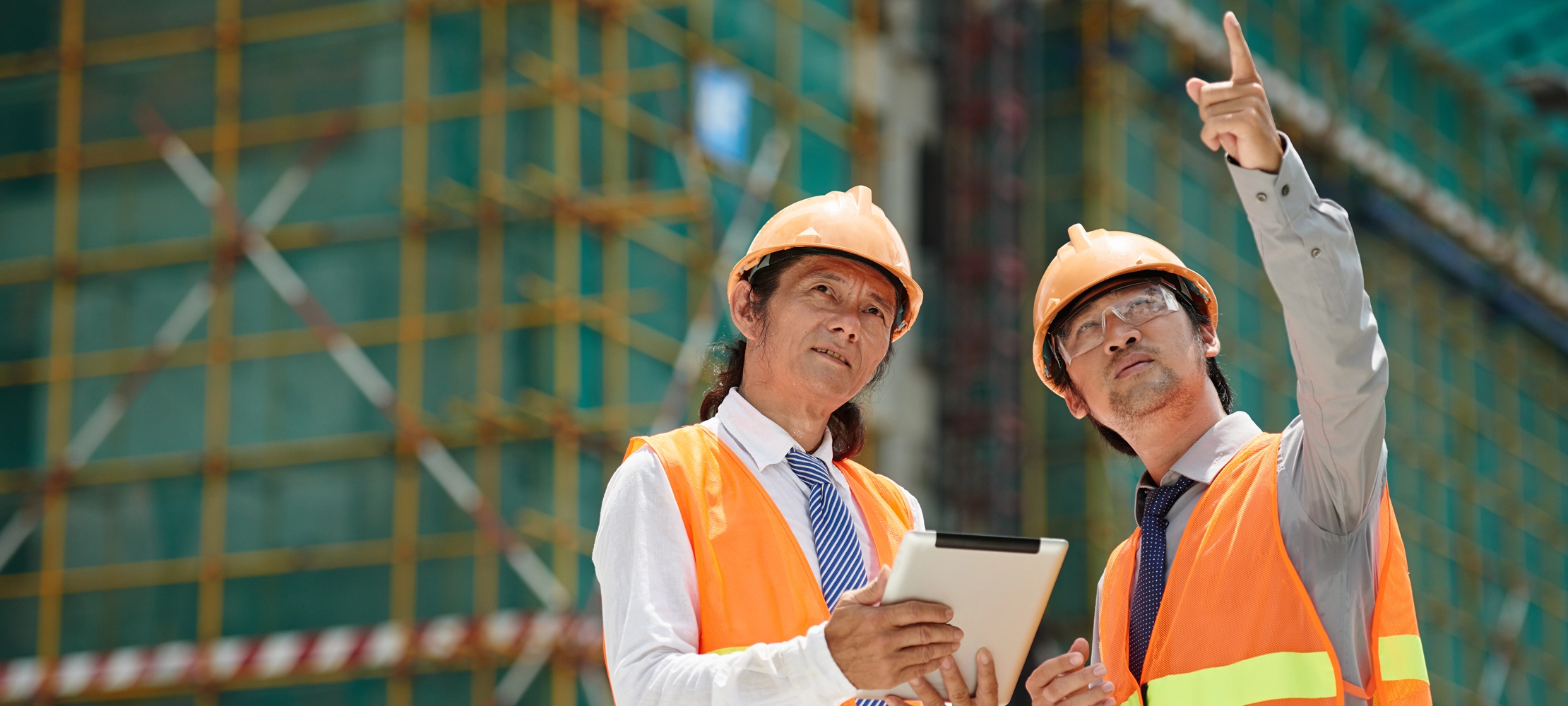
The company adheres to environmental management policies and promotes sustainable construction practices (Green Construction), with a strong focus on addressing climate change and biodiversity conservation.
To ensure sustainability across its supply chain, the company prioritizes sourcing eco-friendly materials, selecting energy-efficient resources, and implementing guidelines for material reuse and recycling. These efforts help reduce reliance on new raw materials and minimize construction waste. Additionally, the company is committed to lowering greenhouse gas emissions by avoiding construction materials that release volatile organic compounds (VOCs) and eliminating the use of asbestos-based materials. These sustainability initiatives align with the principles of Life Cycle Assessment (LCA), which evaluates the environmental impact of materials throughout their entire life cycle. The company complies with ISO 9001:2015 quality management standards and emphasizes procurement practices that meet customer specifications. Every project management team is required to develop operational plans and maintenance strategies to mitigate environmental and community impacts. Furthermore, a continuous quality assurance system is in place to uphold high standards and build confidence among stakeholders.
The company offers a 36-month construction quality warranty to assure both clients and end users. This warranty includes quality inspections and the correction of any defects that may arise after construction, ensuring the project's strength, durability, and overall quality.
Guidelines for reusing materials and selecting environmentally friendly materials.
The quality of construction materials is a key determinant of structural safety, durability, and operational efficiency. CH. Karnchang has developed rigorous standards and best practices for concrete formwork to ensure compliance with prescribed safety and quality regulations.
Standards and Best Practice Guidelines
Material Selection | Quality Control Process |
---|---|
|
|
CH. Karnchang has developed guidelines to maximize material efficiency in its operations through structured construction planning and the safe reuse of materials. Examples of these practices include treating formwork wood with chemical preservatives or release agents to extend its lifespan and constructing worker accommodations using reclaimed materials that remain safe and of good quality.
Before the construction
- Ensure the formwork is secure before placing the reinforcing steel.
- Clean the formwork to remove any debris or contaminants.
- Do not place heavy construction materials on the formwork to prevent damage.
Under construction
- Install leveling devices to keep the formwork stable and prevent any movement during concrete pouring.
- Continuously monitor the strength of the formwork while pouring concrete, and if any settlement occurs, take immediate corrective action.
After the construction was completed
- The removal of formwork must follow the specified curing period. For example, the side forms of beams, columns, walls, and foundations should remain in place for at least two days before removal.
- After removing the formwork, additional bracing must be installed to support the structure’s weight.
- The concrete surface should be inspected, and any defects must be corrected as necessary.
In addition, the company has launched a pilot test for collecting and analyzing material usage data through the SAP: Controlling System. This initiative aims to optimize material usage planning for greater efficiency. Following the completion of the pilot project, the company plans to fully implement the SAP: Controlling System across all operations.
Integrating Life Cycle Assessment (LCA) in Product and System Design
CH. Karnchang employs Life Cycle Assessment (LCA) as a key tool for reporting analysis and evaluation of environmental impacts and use in planning across every stage of a product or system’s life cycle in construction projects—from material sourcing and production to transportation, usage, and disposal. By utilizing LCA, the company can plan and design with sustainability in mind, focusing on reducing resource and energy consumption, minimizing waste and pollution, and prioritizing the use of eco-friendly materials such as recycled or low-impact alternatives. Additionally, LCA data helps refine construction processes and waste management practices, aligning with Sustainable Development Goals (SDGs), enhancing competitiveness, and ensuring a balance between infrastructure development and long-term environmental conservation.
Target
In 2024, construction began on the Nan City Art and Cultural Center and the Eastern Lanna Art and Cultural Learning Center, with a strong focus on sustainable development. The project prioritizes both social and environmental aspects, particularly by incorporating a designated percentage of recycled and locally sourced materials.
Key Performance Indicators (KPIs) / Goals | Performance Results for 2024 | Certification |
---|---|---|
|
CH. Karnchang has successfully met the specified benchmarks and targets outlined in the procurement contract by undergoing verification through the Material Checklist. Additionally, materials are inspected for compliance with environmental standards, including:
|
|