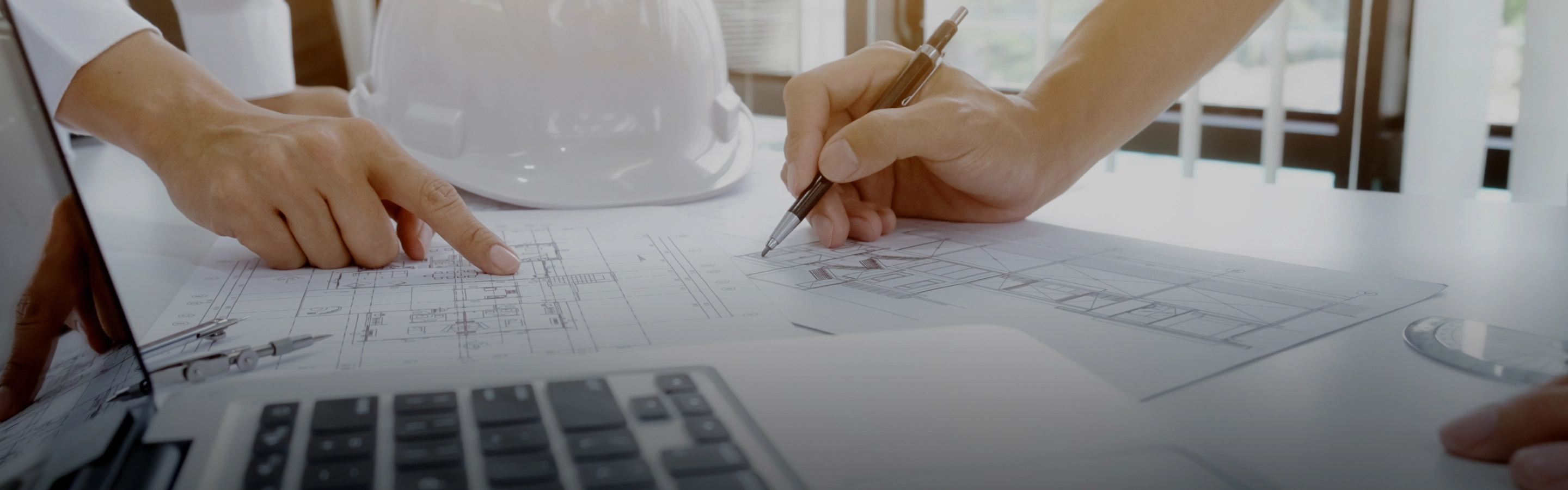
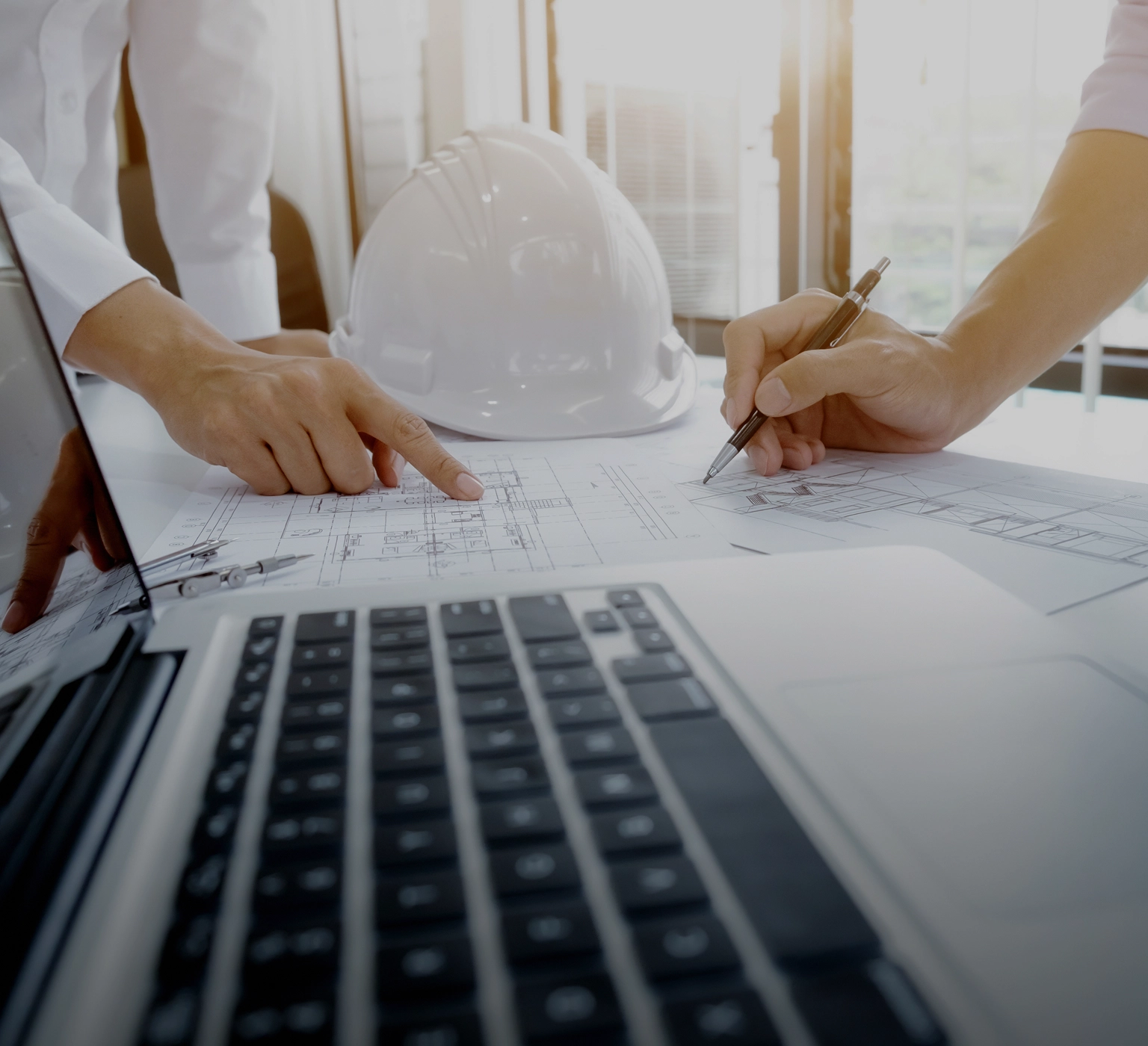
Supply Chain Management
Commitment, Challenge and Opportunity
CH. Karnchang prioritizes sustainable supply chain management, acknowledging its critical role in strengthening operational resilience and mitigating long-term risks. Despite the potential for increased short-term costs, this strategic approach contributes to long-term cost efficiency. To ensure adherence to industry standards and regulatory frameworks, the company has implemented stringent screening and assessment mechanisms for suppliers and contractors. Furthermore, financial risk management is reinforced through a transparent and structured payment policy. Concurrently, the company remains committed to advancing occupational health and safety by fostering awareness and systematically enhancing workplace safety measures for employees and contractors.
Beyond its commitment to mitigating supply chain impacts across all dimensions, the company actively promotes local employment and economic development while advancing the adoption of environmentally sustainable products. These strategic initiatives not only strengthen credibility among both public and private sector clients but also contribute to shareholder and investor confidence by reducing supply chain risks. This approach exemplifies the company’s dedication to fostering shared value with all stakeholders, ensuring long-term sustainability and balanced economic growth.
Supporting the SDGs Goals
Goal 8:
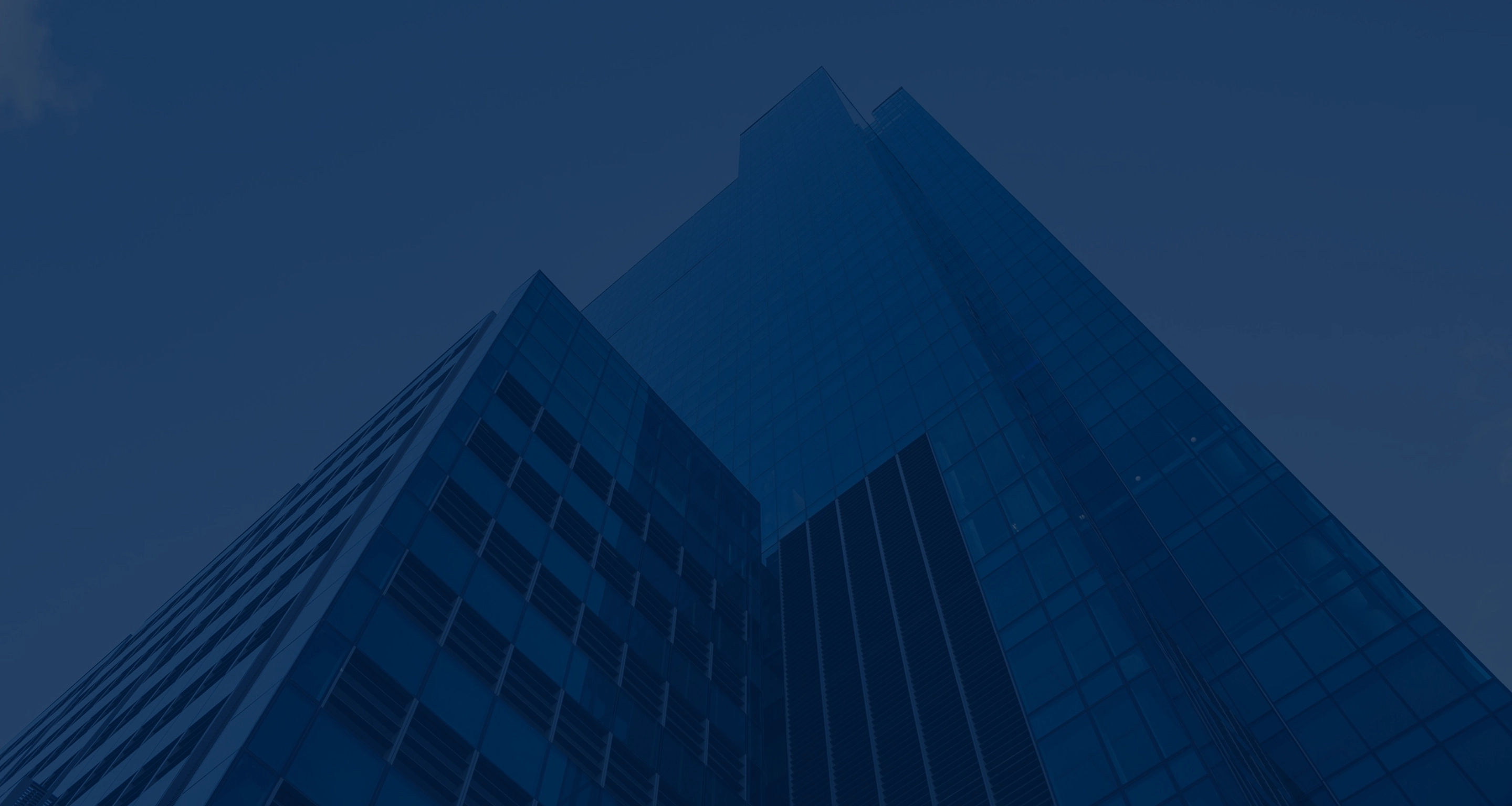
Stakeholders Directly Impacted
Goals and Performance Highlights
- The partners acknowledge and comply with the code of conduct.
- The company conducts evaluations for 100% of its partners.
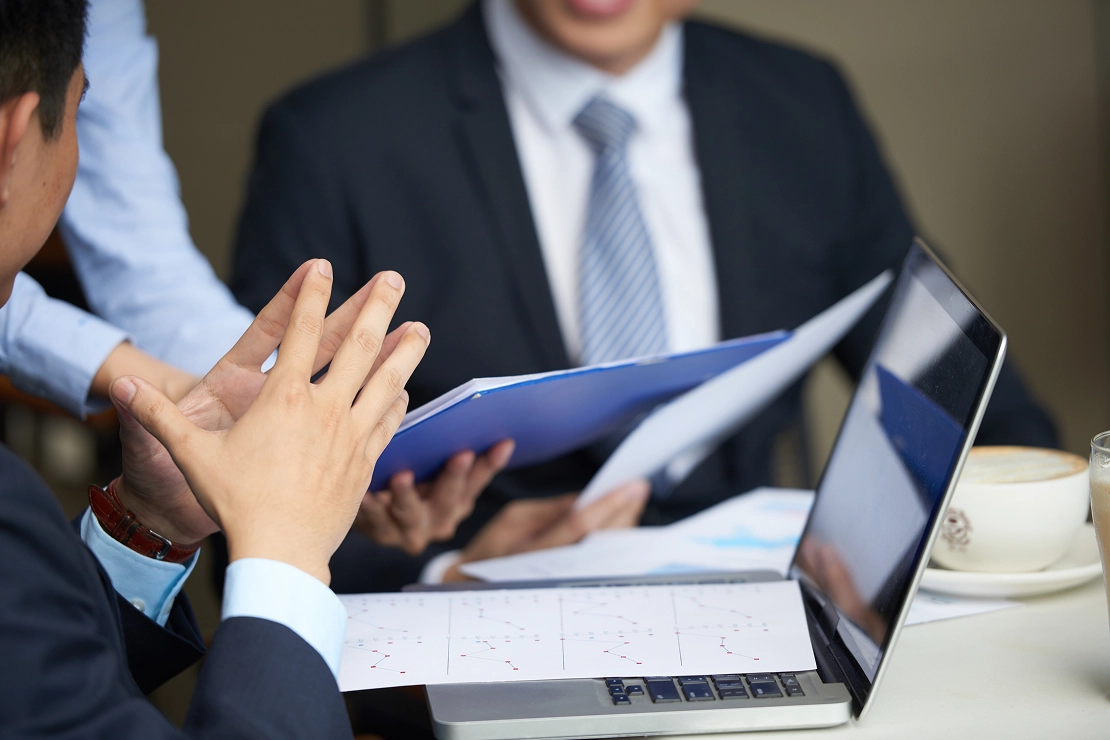
Management and Operational Approach
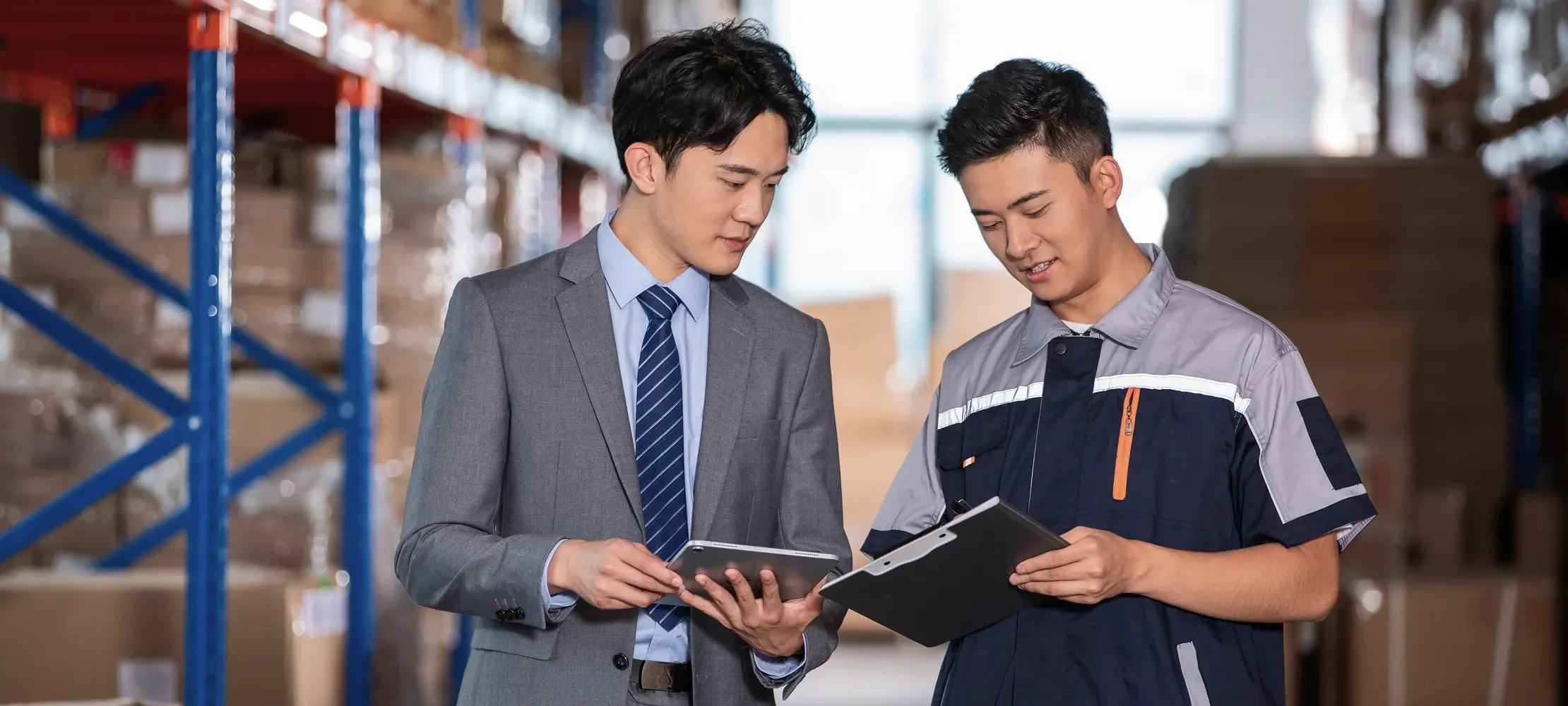
The company is committed to sustainability in the supply chain by prioritizing environmental, social, and governance (ESG) impacts under a sustainable procurement policy and supplier code of conduct.
A working group has been established under the Corporate Governance and Risk Management Committee to continuously review risks and develop response plans at both the corporate level and business level, with the Chief Executive Officer (CEO) setting directions and monitoring performance. Meanwhile, operational units, such as the procurement department, are responsible for supplier selection and management, the facilities management department ensures contractor safety, and the internal audit department focuses on transparency. All units collaborate to enhance efficiency and sustainability in the supply chain.
Sustainable Procurement Policy
The company prioritizes sustainable procurement as a fundamental aspect of its business operations. It is committed to ensuring that supply chain management adheres to legal requirements and industry standards while maintaining transparency, integrity, and accountability. Furthermore, the company considers the environmental, social, and governance (ESG) impacts of its procurement practices. All executives and employees are responsible for upholding and strictly adhering to this sustainable procurement policy.
Procurement in accordance with established criteria
Consideration is given to needs, price, service, and product quality for the maximum benefit of the company.
Business Ethics
Procurement and purchasing by providing accurate and clear information to partners equally and fairly.
A Transparent and Accountable Selection Process
A fair and auditable competition is ensured, with full compliance with all applicable regulations and legal requirements.
Advancing Green Procurement Initiatives
The company is committed to promoting sustainable procurement practices by prioritizing environmentally responsible sourcing. This includes procuring goods from local and domestic suppliers to strengthen the local economy while minimizing environmental impact. Additionally, the company actively supports the adoption of eco-certified products that comply with international environmental standards, such as ISO 14001, to enhance sustainability throughout the supply chain.
Clearly Defined Terms and Conditions
Clearly define the contractual terms and conditions to ensure mutual understanding and fairness, fostering transparency and accountability in accordance with sustainability and governance principles.
Human Rights
The company is committed to engaging with business partners who uphold human rights, ensure equitable treatment of employees, and strictly oppose any form of forced labor.
Business Ethics and Supplier Code of Conduct
The company has implemented a Supplier Code of Conduct to align its procurement processes with internationally recognized ethical, social, and environmental standards. This framework establishes a compliance benchmark for selecting and evaluating both current and new suppliers, ensuring adherence to principles of corporate governance, human rights, fair labor practices, workplace health and safety, and environmental stewardship. All suppliers are required to meet or exceed legal and regulatory standards, reinforcing the company’s commitment to sustainable and responsible business operations. The company encourages its partners to sign and implement the Supplier Code of Conduct, ensuring that it is put into practice effectively. It also fosters collaboration with partners to identify appropriate practices, assess their capabilities, and monitor their performance to ensure compliance with established standards and business ethics. Additionally, the company holds regular annual meetings with key partners.
Screening of New Approved Vendor and Current Approved Vendor
The company has a formal procedure for selecting both new and current procurement vendors, which involves evaluating their capabilities in terms of products and services, as well as addressing key factors related to environmental sustainability, social responsibility, human rights, labor rights, and corporate governance (Environmental, Social, and Governance: ESG). These factors include the vendor's ability to meet delivery requirements, comply with applicable laws, adhere to international human rights standards, obtain environmental certifications, and maintain workplace safety. This evaluation is conducted through the new vendor and subcontractor qualification assessments, reflecting the company’s commitment to building a sustainable and responsible supply chain.
The company has developed a set of criteria for selecting new vendors (New Approved Vendor) and evaluating current vendors (Current Approved Vendor) in accordance with its procurement policy. This evaluation process incorporates assessments of both the quality of products and services, as well as sustainability performance, covering key sustainability issues across the following three dimensions:
- Social Rights, Human Rights, and Labor Rights dimension: This section emphasizes the importance of ensuring that human rights are respected and affirms the fair treatment of employees in compliance with all applicable labor and human rights laws, covering aspects such as worker protection, wages, compensation, allowances, and social security contributions. Furthermore, intellectual property rights must be upheld. A safe, suitable, and well-organized work environment must be provided, along with ongoing monitoring, impact assessments, and the establishment of both short- and long-term risk management plans.
- Environment dimension: The emphasis is on adhering to applicable laws, critical standards, and environmental regulations, prioritizing the management of waste and pollution, along with the effective use of resources to minimize adverse environmental impacts.
- Business Ethics dimension: This principle emphasizes the importance of conducting business with ethical integrity, transparency, and in full compliance with applicable laws. It involves the disclosure of necessary business information, including risk management strategies and the safeguarding of intellectual property. Additionally, the systematic tracking of project and contract histories is integral to this approach. Furthermore, fostering an environment for the exchange of knowledge and experiences is key to driving collaborative business innovation, which is central to developing a sustainable supply chain that aligns with global sustainability goals.
Monitor compliance with the Supplier Code of Conduct
Which addresses key social and environmental concerns. The company has established a set of evaluation criteria for suppliers, which are divided into four critical areas:
The company has established selection criteria for approved vendors in procurement, which include the following social and environmental considerations, aligned with sustainable development goals (SDGs) and environmental, social, and governance (ESG) principles.
- Ethical Standards: Ensuring compliance with legal regulations, contractual obligations, and mutual agreements, in alignment with the principles of sustainable development.
- Safety Measures: Compliance with workplace safety regulations, encompassing the proper organization of equipment and the implementation of standardized work procedures, in line with sustainable development goals and environmental, social, and governance (ESG) standards.
- Environmental Aspects: Management of dust control and pollution arising from construction activities, as well as the proper disposal of construction waste.
Monitor compliance with the Supplier Code of Conduct, which addresses key social and environmental concerns
The company has established a set of evaluation criteria for suppliers, which are divided into four critical areas:
The allocation of evaluation criteria in this context underscores the prioritization of product quality as the primary consideration, aiming to reduce operational risks and minimize the costs associated with potential rework. Secondary importance is placed on delivery, highlighting the significance of time management within construction projects. The evaluation of coordination and responsibility serves to identify and cultivate partners who exhibit ethical practices and professionalism, ensuring the development of sustainable, long-term partnerships aligned with the principles of sustainable development and corporate social responsibility (CSR).
Key Supplier Analysis
The company classifies its suppliers into three categories: Critical Tier 1 Suppliers, Non-Critical Tier 1 Suppliers, and Critical Non-Tier 1 Suppliers (suppliers that do not engage directly with the company). This classification is based on Spend Analysis (evaluation of expenditure), Critical Analysis (assessment of the importance of products or services in procurement), and Dependent Analysis (measurement of reliance on suppliers). This structured approach allows the company to develop informed operational strategies and efficiently assess supplier-related risks. The company’s suppliers are categorized into Critical Tier 1 Suppliers, who provide essential materials, and Non-Critical Tier 1 Suppliers, who supply general goods and services. These include contractors, machinery suppliers, material and equipment distributors, waste management firms, and logistics providers, among others.
Key Indicator | Year 2024 |
---|---|
Total Tier 1 Suppliers (Critical Tier 1 Suppliers) | 1,597 suppliers (27 critical suppliers) |
Vendors (Critical Vendors) | 479 vendors (11 critical vendors) |
Contractors (Critical Contractors) | 1,118 contractors (16 critical contractors) |
Supplier Risk Assessment and Management
The company’s supplier risk management strategy, including supplier development plans, is implemented to assess and mitigate risks associated with suppliers, ensuring minimal impact on business operations while reducing environmental, social, and governance (ESG) risks across the supply chain. The assessment covers economic factors such as product quality, timely delivery, and service coordination, alongside sustainability criteria, including ethical business practices, labor and human rights compliance, environmental management, and corporate social responsibility (CSR) toward communities and society. The company implements a rigorous evaluation process for all business partners (100%), assessing both corporate-level and operational risks concerning environmental, social, and corporate governance (ESG) criteria. Each assessment area is detailed as follows :
Economic Risk Assessment
Risk Management and Risk from Project Delays: Project delays can stem from the project owner, contractor, or other unforeseen circumstances, particularly disruptions in supply chain logistics and procurement. A critical risk factor is the shortage of construction materials, which can significantly impact project timelines. To mitigate these risks, the company implements proactive procurement strategies by securing long-term supply agreements for essential materials such as cement and steel. This approach ensures resource availability for projects with signed contracts and minimizes potential disruptions due to material shortages.
Management Strategy: As part of its proactive supply chain management, the company has entered into advance procurement agreements for key construction materials. This includes securing contracts for cement and steel to ensure seamless execution of projects with finalized contractual commitments.
Risk Factors Related to Construction Material Costs, Labor Costs, and Oil Price Volatility: The management of construction contracts directly impacts gross profit, relying on precise cost estimation and effective cost control to align actual expenses with projections. Key factors influencing cost management include fluctuations in construction material prices, changes in labor costs driven by supply and demand dynamics, and volatility in oil prices, which serves as an indirect cost affecting overall operations.
Management Strategy: The company manages construction projects through two types of contracts
- In cases where construction contracts incorporate price adjustments through an escalation factor (K), this factor is calculated based on variations in production costs. While the formula may not comprehensively account for all increases in raw material and labor costs, it is structured to address unforeseen price escalations, thereby minimizing the impact on overall construction costs. The majority of projects undertaken by the group are for public sector clients.
- For fixed-price or lump-sum construction contracts where the contract does not specify or cannot determine an adjustment factor (K value), this model is primarily used for Turnkey Projects. The total project value typically includes contingency costs to account for fluctuations in construction material prices. These contracts are most commonly used by private sector clients.
Environmental, Social, and Governance (ESG) Risk Assessment
The company conducts an evaluation of its business partners to assess the likelihood and severity of risks associated with environmental, social, and governance (ESG) factors. The assessment provides a detailed analysis of each ESG component as outlined below.
E - Environmental Risk Considerations Key environmental risks include compliance with environmental laws, efforts to mitigate greenhouse gas emissions and combat global warming, management of noise and vibration pollution, responsible water usage and wastewater treatment, energy consumption control, waste and hazardous material management, and adherence to environmental standards through certifications or regulatory compliance (ISO 14000/EIA).
S - Social Risk Factors These include compliance with legal regulations and international human rights standards, workforce management, occupational health and safety, and adherence to relevant laws.
G - Governance-Related Risk Factors The key governance-related risks encompass anti-corruption frameworks, quality assurance and safety measures within production processes, adherence to fair business competition principles, and the protection of intellectual property rights.
In 2024, a comprehensive risk assessment covering economic, environmental, social, and corporate governance (ESG) factors was conducted for all 309 newly engaged business partners, representing 33% of the company’s total business partners. The assessment did not identify any material risks.
Supplier Performance Evaluation
The company has an ongoing process to monitor, audit, and evaluate supplier performance through an annual On-site Audit as part of the Yearly Performance Evaluation. This ensures that suppliers adhere to the company’s operational standards and comply with the Supplier Code of Conduct, relevant legal requirements, and corporate governance principles while minimizing negative impacts on society and the environment.
In 2024, the company conducted on-site audits for four current business partners. These audits included site visits by representatives from the procurement department or relevant user departments (2nd party assessment) and evaluations by an independent certification body (Supplier On-Site Assessment by a Third Party). The assessments were conducted in accordance with internationally recognized standards, such as ISO 9001 and ISO 14001, and covered the following key areas:
- Ethical Standards Adherence to labor laws, human rights principles, and other relevant legislation, as well as the contractual terms and conditions.
- Workplace Safety This encompasses the appropriate work procedures, operational steps, and the utilization of suitable equipment, ensuring a safe working environment in line with best practices for safety standards.
- Environmental management in compliance with established laws, ensuring the proper management of water resources, pollution, waste, and hazardous materials
- Social Responsibility and Community Engagement
In 2024, the company carried out assessments of 134 partners and 58 subcontractors, evaluating criteria such as workforce capacity, machinery, quality, planning, cooperation, and safety. The results of these evaluations were predominantly rated as good or excellent, with no vendors or contractors identified as requiring improvement. Furthermore, in the past year, there have been no reports of operational issues or complaints concerning violations of labor rights, human rights, or breaches of good governance and business ethics.
Grade | Number of Suppliers | Percentage (%) | Number of Subcontractors | Percentage (%) |
---|---|---|---|---|
A Excellent | 93 | 69.40% | 28 | 48.28% |
B Good | 39 | 29.10% | 29 | 50.00% |
C Satisfactory | 2 | 1.49% | 1 | 1.72% |
D Requires further improvement | 0 | 0.00% | 0 | 0.00% |
Total | 134 | 100.00% | 58 | 100.00% |
The company continues to prioritize offering guidance and support to enhance the capabilities of unassessed partners, ensuring that their operations are in alignment with the established standards and stakeholder expectations, while fostering sustainable development throughout the company’s supply chain, in line with its commitment to sustainability and ESG principles.
Payment Management to Partners
Effective credit risk management is a crucial element of the company's operations, as it directly influences the stability and overall performance of the business. To mitigate financial risks, the company has implemented clear debt repayment policies, which are aligned with the payment schedule set by project owners. The company has classified its business partners into distinct categories, namely vendors, subcontractors, and labor contractors. Payment terms are clearly specified within the purchase and work order documents for each group. Labor contractors and smaller subcontractors are typically paid within shorter timeframes compared to larger subcontractors and vendors. It is widely recognized by major vendors that any payment delay exceeding 60 days from the agreed-upon terms could adversely affect both the partners involved and their trust in the company’s credit. In 2024, the company successfully maintained exemplary debt repayment standards, ensuring no payments were overdue by more than 60 days, thereby reinforcing its commitment to financial responsibility in line with sustainable business practices.
Key Indicator | Year 2024 |
---|---|
Single-installment vendors and contractors (average) | 45 days |
Two-installment contractors | 22 days |